Du willst diesen Beitrag hören statt lesen?
Klicke dazu auf den unteren Button, um den Inhalt von Soundcloud zu laden.
Hanf ist seit Menschengedenken beliebt, da die Pflanze für den Menschen komplett nutzbar ist. Heutzutage ist das Thema Nachhaltigkeit in aller Munde. Hanf hat diese Anforderung bereits erfüllt, als diese noch gar nicht formuliert war.
Verarbeitung von Hanf vom Feld bis hin zu den einzelnen Produkten
Alle Bestandteile des Hanfes können zu 100 % verwertet werden. Die komplette Verarbeitung erfolgt rein mechanisch. Die Samen werden gleichzeitig mit dem Stroh geerntet und unmittelbar nach ihrer Ernte zum Trocknen gebracht. Das Stroh bleibt noch ca. 3 Wochen auf dem Feld zur sogenannten Feldröste liegen, bevor es in Quaderballen gepresst zur Faseraufbereitungsanlage transportiert wird. Dort erfolgt der Aufschluss des Hanfstrohs in Fasern und Schäben.
Für Hanfprodukte ist die heutzutage übliche industrielle (automatisierte) Weiterverarbeitung eine echte Herausforderung. Die gängigen Produkte verlangen heute eine kontinuierlich gleichbleibende Form und Ausstattung der Vorprodukte. Da es sich bei Hanf um ein Naturprodukt handelt, welches in Form und Ausführung von verschiedensten, nicht zu beeinflussenden Faktoren abhängig ist, stellt der möglichst gleichbleibende Produktions-Ausstoß die industrielle Aufarbeitung vor große Herausforderungen, welche nur durch große Erfahrung bewältigt werden können.
Die Qualitätsparameter wie Röstgrad, Reinheit, Feinheit und Reißfestigkeit der Faser sind mehr von den Anbaubedingungen wie Bodenbeschaffenheit, Wasserverfügbarkeit und Wetter abhängig, als von den angebauten Sorten selbst. Nicht alle Parameter sind beeinflussbar, umso wichtiger ist es deshalb bei der Aufbereitung die Qualitäten im richtigen Verhältnis abzumischen.
Ein erster Faktor ist die sogenannte Röste. Feldröste wird der Prozess genannt, der nach dem Abschneiden des Hanfstängels, während dieser dann auf dem Feld verbleibt, stattfindet, bei dem durch mikrobakterielle Prozesse schon die ersten Beeinflussungen der faserigen Anteile bestimmt werden. Wenn dieser Prozess zu lange stattfindet, wird die Faser zerstört, aber wenn man zum richtigen Zeitpunkt das Material in der richtigen Trockenheit einbringt, dann hat man gute Chancen, dass die Aufarbeitung möglich ist. Um den richtigen Zeitpunkt der Röste zu bestimmen, bedarf es der Erfahrung des Anbauers.
In früheren Zeiten wurde der Feldrösteprozess als Wasserröste in stehenden oder fließenden Gewässern durchgeführt. Dies kann heute aufgrund der generell starken Gewässerbelastung nicht mehr stattfinden. Deshalb wurde komplett auf die Feldröste umgestellt. Der Nachteil der Feldröste ist: Diese ist aufgrund der wechselnden Witterungseinflüsse nicht hundertprozentig kontrollierbar.
Der Röstgrad definiert sich durch die unterschiedlich langen mikrobakteriellen Prozesse und wird durch die Farbe des Strohs von hellblond bis dunkelgrau dargestellt. Über eine definierte Farbkarte ist dieser Röstgrad visuell sehr gut bestimmbar. Wenn man weiß, was aus dem gerösteten Hanfmaterial später hergestellt werden soll, kann man zum exakt richtigen Röstgrad den Hanf vom Feld nehmen.
Die Reinheit wird über den Restschäbengehalt bestimmt. Je besser die Aufbereitung funktioniert, desto weniger Schäben und Staubanteile sind in der Faser. Der Restschäbengehalt wird prozentual und per manuellem Auszählen definiert und sollte bei einer guten Faser für z. B. den Automobil-Bereich unter 3 % liegen. Ein kleiner Ausflug in die Linguistik: das wohlbekannte Worte „schäbig“ für schlechte Qualität stammt aus früherer Zeit. Wenn die Faseranteile zu viele Schäben enthielten, bezeichnete man das Material als „schäbig“. D. h., wenn Fasern Schäben enthalten, sind sie schäbig – ergo nicht so gut. Daraus entwickelte sich der Begriff „Schäben“.
Die Feinheit von Fasern wird je nach Anwendungsgebiet mit Kunden definiert und über visuelle Vergleiche mit Masterchargen abgeglichen.
Reißfestigkeit wird meist im fertigen Produkt (Faservlies) anhand verschiedener Zugproben kontrolliert. Wenn der Röstgrad zu hoch ist, kann es aufgrund der weit fortgeschrittenen Abbauprozesse zu Festigkeitsverlusten kommen. In aller Regel ist aber in Bezug auf Festigkeit der Hanf anderen Faserpflanzen deutlich überlegen.
Industrielle Produkte: Hanfaufbereitung ist zuallererst die Trennung von Fasern und Schäben. Als Erstes muss die Stängelstruktur des Hanfes aufgebrochen werden, um die Fasern von den Schäben zu lösen. Dies geschieht durch Grobbrecher und/oder Hammermühlen, anschließend durch Feinbrecherwalzen. Nach jedem brechenden Schritt kommt eine mit verschiedenen Mechanismen gestaltete Ausreinigung. Dieser Vorgang wird so lange wiederholt, bis die gewünschte Reinheit erreicht wird. Anschließend werden durch kämmende Prozesse die Faserbündel mechanisch in dünnere Faserbündel aufgetrennt und mit weiteren Siebprozessen Unreinheiten entfernt. Dies wird so lange wiederholt, bis die gewünschte Feinheit und Reinheit erreicht wird. Eine gewisse Vorsicht ist geboten. Falls der mechanische Einfluss zu stark ist, kann es zu Faserschädigungen kommen. Die im Prozess herausgelösten Schäben werden über verschiedene Siebprozesse auch von den Restfasern und Stäuben befreit und dadurch zu vermarktbaren Produkten in den Bereichen Tiereinstreu, Mulchmaterial und Schüttdämmung eingesetzt. Dabei ist meist eine weitere Zerkleinerung oder Kalibrierung nötig. Die Schäben werden in der Regel in 200 Liter Säcken abgefüllt oder eingepresst. Die Fasern werden in drahtgebundene Faserballen zu 100 bis 200 kg verpresst. Die bei diesem Prozess entstehenden Nebenprodukte (Stäube) kann man brikettieren und als Brennstoff verwerten. Ein grobes Ausbeuteschema bei dem oben geschilderten Prozess liegt bei ca. 25 % verwertbaren Fasern, ca. 60 % sauberen Schäben und 15 % Stäuben. Damit ist die Komplettverwertung des Hanfstrohs gesichert.
Die Aufbereitung ist also eine Aneinanderreihung von mechanischen Trennprozessen wie brechen und schlagen, begleitet von Sortier- und Siebeinheiten. Oft wurde in der Vergangenheit versucht, dies mit einigen wenigen Maschinen zu realisieren, aber gute Qualität ist nur erreichbar mit der entsprechend hohen Anzahl von Verarbeitungsschritten.
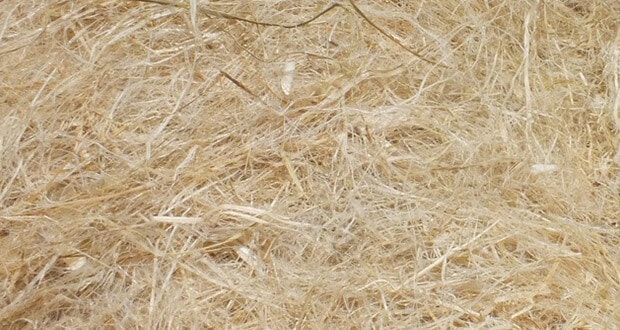
Technische Fasern: Einsatz z. B. in der Automobilindustrie (Türverkleidungen) oder bei der Gebäudedämmung.
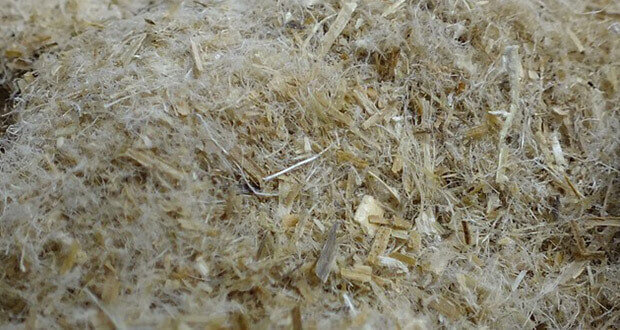
Super-Kurz-Fasern: z. B. für die Herstellung von Bremsbelägen in der Automobilindustrie
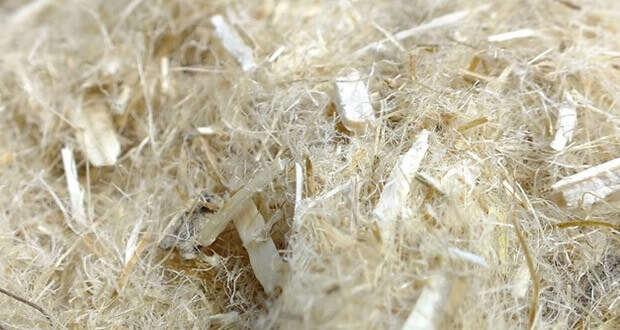
Kurz-Fasern: z.B. für die Herstellung von Spezialpapieren in der Papierindustrie
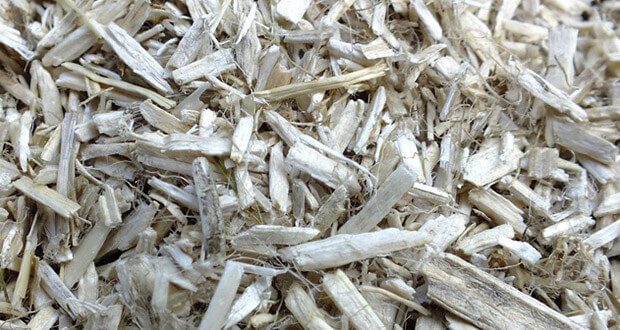
Schäben: Einsatz z. B. als Mulch, Tiereinstreu oder in der Bauindustrie.
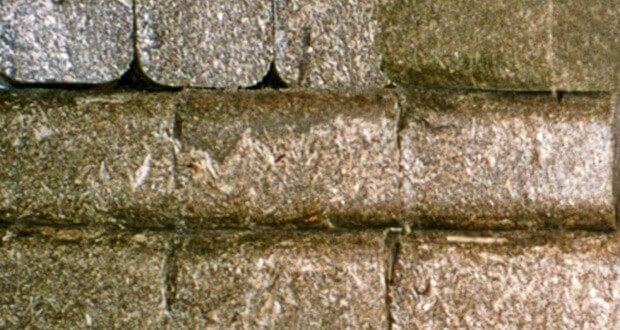
Staub: Einsatz z. B. als Hanfbriketts zum Heizen.
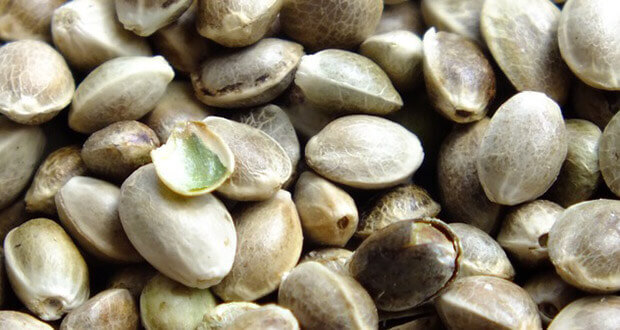
Hanfsamen: Die Öle sind auch gut für Farbmittelherstellung, Bio-Verbundstoffe usw.
Die BAFA Badische Naturfaseraufbereitung GmbH (Geschäftsführer: Bernd Frank) wurde 1996, im Jahr der Wieder-Legalisierung des Nutzhanf-Anbaus, gegründet. Als Bindeglied zwischen Landwirtschaft und Industrie bereitete die BAFA als erste deutsche Hanffaseraufbereitung einheimisches Hanfstroh mechanisch in Fasern und Schäben auf.
Ebenso widmete man sich schon gleich von Beginn an den Bereichen Saatgutvermehrung, Aussaat und Ernte sowie der industriellen Verarbeitung und Vermarktung der gewonnenen Produkte. Es gab viel zu entwickeln, denn durch die jahrzehntelange Verbannung war viel Wissen über diese tausende Jahre alte Kulturpflanze verloren gegangen. Im industriell-mechanischen Produktionsprozess werden Fasern von Schäben getrennt und die Faserfraktionen abnehmergerecht konfektioniert der weiterverarbeitenden Industrie geliefert. Die Schäben werden ausgereinigt, entstaubt und abgesackt als Tiereinstreu vertrieben.
Außerdem beteiligt sich die BAFA aktiv an Produktentwicklungen aus Fasern und Schäben, um den Markt für Hanf breiter zu gestalten. So hat die BAFA maßgeblich zu der Entwicklung und Bauzulassung der Thermo-Hanf-Matte, dem ersten zugelassenen Hanfdämmstoff in Deutschland, beigetragen. Ebenso ist die BAFA an der Entwicklung von spritzgussfähigen Hanffaser-PP-Pellets sowie verschiedenster anderer Anwendungsfälle beteiligt.
Auch in der Erntetechnik war Pionierarbeit gefragt. In Zusammenarbeit mit den Partnern Götz Landtechnik GmbH, Deutz-Fahr GmbH und der Landesanstalt für Pflanzenbau wurde der sogenannte Hanfvollernter entwickelt. Dieser kam im Jahr 2000 erstmalig zum Einsatz und erhöht seither die Wirtschaftlichkeit des Hanfanbaus ungemein, da er von einer Anbaufläche in nur einem Arbeitsschritt sowohl das Stroh als auch die in jeder Hinsicht wertvollen Hanfsamen ernten kann. Von diesem Hanfvollernter sind heute schon 20 Stück in ganz Europa im Einsatz.
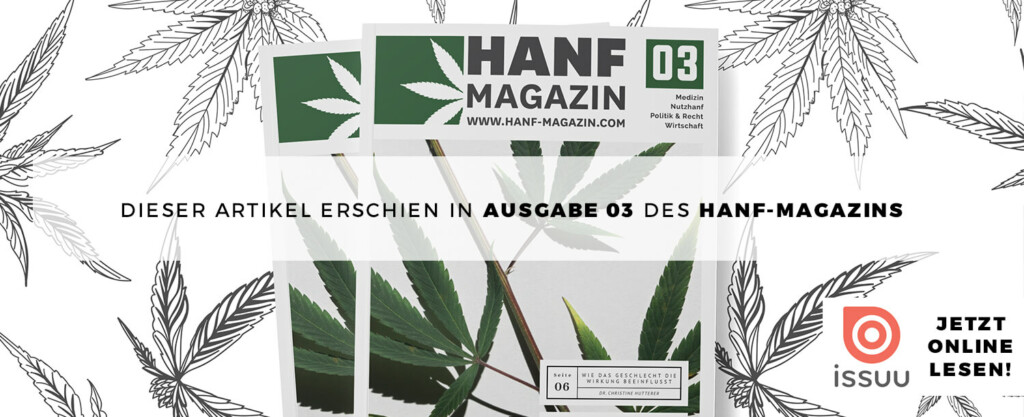